HANDWOVEN TAPESTRY
inspired by
the beautiful white Siberian tigress,
Sabrina
designed
and orchestrated by
Leslie Kiser
and
woven by the designer,
as well as
a multitude
of
tapestry
students,
friends in need,
and
casual
passers-by
while under construction at
Woolenworks
in McKinney, Texas,
1995-1998.
---o)(o---
A TIGRESS IN TEXAS
A Rare Creature Portrayed in a Rare Medium
Above is the 7 1/2 by 4 foot handwoven tapestry, A Tigress in Texas, pictured still attached to its primitive loom.
You might wonder, "Why a SIBERIAN tiger in a NORTH TEXAS landscape?" While the main focus of this website is to document the construction of this weaving, it is hoped to also stimulate an awareness of the plight of many endangered species, as represented by the beautiful tigress, Sabrina of the Texas Exotic Felne Foundation.
---o)(o---
For most, the word "tapestry" conjures up images of drafty Medieval castles with monumental handwoven pictoral wall hangings. Many would be surprised to know that in our world of assembly-line mass-production, there still exists a small number of artisans dedicated to the creation of tapestries using the techniques perfected hundreds of years ago.
---o)(o---
---o)(o---
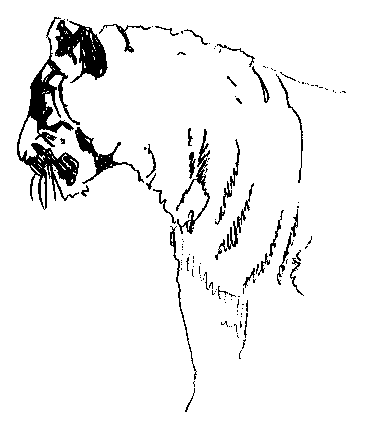
---o)(o---
But let's go
back to the beginning.
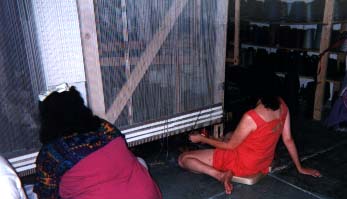
The
weaving starts at the bottom and at first we must sit
on the ground. Outside, it's a typical
Texas upper 90 degree plus summer, but the cement floor
of Woolenworks in McKinney is amazingly cool.
---o)(o---
The loom consists of
three vertical 2 x 4's, a diagonal to keep it "square",
and
two horizontal notched beams to hold the warp evenly
spaced. (The warp is the white vertical string
stretched tightly up and down between the
horizontals that
provides the foundation for the weaving.)
With
seven
feet of weaving width, there is elbow room for three
weavers, although at times, the design forces one or
more weavers to wait for an adjacent area to be
completed before they can proceed, somewhat like laying
bricks.
---o)(o---
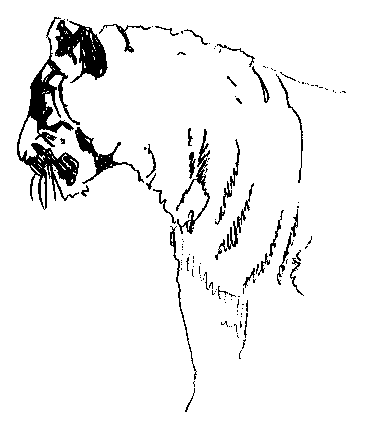
As the weaving progresses we must elevate ourselves to
the current working level by sitting on gradually
taller pillows and chairs. Eventually we will stand on
step stools to reach the highest areas.
If this were a more sophisticated (and expensive) loom,
the weaving itself would be advanced to keep the
working level even with the weavers, not unlike film in
a camera.
However, I prefer this primitive frame loom for
numerous reasons, the most important of which is that
you can see the entire image area while you work,
making subsequent design choices
easier.
Otherwise, only
a small section of the work
is visible, making it necessary to continually "rewind"
to view the progress or photograph the piece for
reference as you go.

Here's the back of the tapestry. All the weaving has
been completed and it has been cut from the loom, but
there is still plenty of work to
do.
All of the warp ends must be secured using
the
damascus knot. At 3 1/2 warp ends per inch (think
pixels, if you're computer literate), that's 2940
warp ends and 2939 knots. And that's just the top!!
There are just as
many knots to tie on the bottom as well.
The top and bottom fold overs must be, ....
ummmmh well .... , folded over to provide a firm,
solid foundation for mounting on a horizontal board.
Using not so ancient techniques involving velcro and
(shudder) hot glue, the piece is truely finished and
ready for installation.
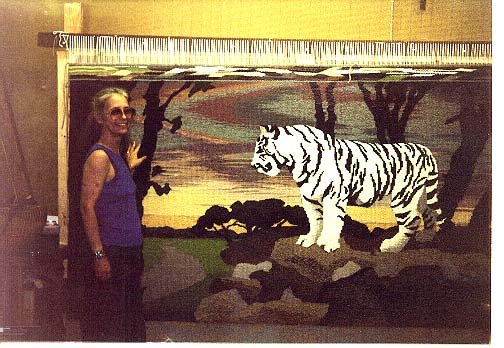
This should
provide some scale.

This link takes you to
Bryan Livingston's Online Graphics
Generator.